Mechanical Products - Gun Drills.
|
Gundrill
|
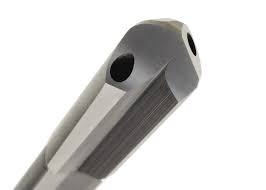 |
Gun-Drills Make Deep-Hole drilling more efficient and easy for you. Deep-Hole Drill, as initially invented for ‘Gun-Drilling’ application in Europe during the Second World War; and since then is popular as ‘Gun-Drill. However, over last 75 year, its applications are extended in Auto and other engineering metal cutting industries for Deep Hole Drilling. Still these Deep-Hole Drills are yet popular and called as ‘Gun-Drills’, even if used for other applications. Accusharp Cutting Tools have entered into this new segment of Round Tools for Deep-Hole Drilling applications; and call them as ‘Gun-Drills’. The applications are like deep holes drilling on Crankshaft, Engine blocks, Machine Tools, etc. Standard geometry for single lip Gun-Drill drill has been shown herewith. However, it may change according to its applications for different work materials, and machining parameters. Moreover, any change in the cutting edge geometry will have effect on bore surface finish, geometrical accuracy, drill centring, chip shape, chip removal, process reliability, and useful life of the drill, etc. Our standard grinding geometry can take care of virtually all drilling operations successfully. However, we design and manufacture Gun-Drills with special geometry for deep drilling long chipping material or material that is difficult to machine We manufacture and supply Gun-Drills in the range of Dia. 4 to 30 mm., having length up to 1000 mm. |
|
Company Prodcut:Accusharp Cutting Tools |
Gundrilling
|
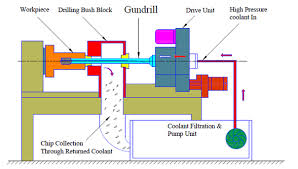 |
Metal cutting ‘Round ToolsÂ’ like Carbide and H.S.S. drills, end-mills, reamers, cutters, burrs, form tools, step drills, etc. As a matter of fact, it is difficult to drill a straight and accurate dimensional hole of a depth more than about five times the diameter using a standard twist drill. However, using a ‘GundrillÂ’ one can make a ‘DeepÂ’ hole of much longer depth; even 200 times the drill diameter. Not only it drills 200 times deep, but also with the precision tolerance of hole size, roundness, straightness, concentricity and surface finish in one pass. As it can cut small diameter and long length holes, the Gundrill can be also suitable for very deep hole drilling to machine parts as up to a 300:1 depth-to-diameter ratio. This typical drill was initially developed 100 years back in Germany, to drill Gun barrels having 5.56 mm (0.223 inch) bore caliber barrel of rifles with 508 mm (20 inches) length, - nearly 100 times the diameter of the bore. The Gundrill was developed to drill such long, straight holes of high accuracy dimensional requirements. And since then, this type of drill is known as ‘GundrillÂ’, even if subsequently it is being used for other industry requirements and applications. Because of the high capabilities of this innovative ‘Deep Hole Drilling ConceptÂ’, it was but natural, that various industrial sectors got attracted to assess its appropriate extended use for their metal cutting applications. And since then it became widely popular in other industry sectors, as well. Gundrilling is an ideal solution for most of the deep and high precision drilling projects. This operation produces deep holes with precision, high surface finish, and can maintain repeatability of the process. Looking at the present increasing need from various industry sectors, those who are in metal cutting, Accusharp, this year, decided to make ‘GundrillsÂ’ to meet the industry requirements. More about ‘GundrillÂ’ for Deep-Hole Drilling: Gundrills can make holes of exact specified size, with precision tolerances, produce burr-free holes. It can also be used with special formed shapes in blind holes for bottom forming with a minimum of machine revisions. Gundrilling can be done on CNC machining centers, lathes and milling machines with relatively small investment. The process can be made affordable even for small shops with their various production requirements. Gundrill Construction: Gundrills consist of three elements: 1) a carbide tip, 2) a heat treated alloy shank, and 3) a steel driver -Typically silver brazed together and ground as one precision unit. Carbide Tip Driver Carbide Tip Driver Shank Carbide Tip: This is the most critical element of a Gundrill, made of special grade of Tungsten Carbide. Tip pilots the drill through the work piece and cuts the hole of precision dimensional properties. The drill-point, or nose geometry has two basic angles which may vary according to the work material and process parameters. These angles balance cutting forces on the bearing bush to keep the drill concentric. The tip diameter is slightly larger than the shank diameter, so that the shank can rotate freely without touching the hole. A round, kidney-shaped, or two round holes through the tip are provided through which high pressure coolant passes continuously during the drilling operation. Gundrill Tip can be resharpened several times to extend their life. Shank: The shank is made of special alloy steel tubing with a110° -120° Vee-flute formed to the centre of the shankÂ’s diameter. Coolant is forced from the driver through the centre of the shank towards the tip, there from it is flushed back along the shankÂ’s flute. The shank has to maintain Gundrill alignment; and therefore it should be strong enough to absorb cutting torque and thrust. If the shank is too stiff it may transfer minor mis-alignment in the entire tool set up. However, if the shank is more flexible, it may sag at high RPMs. Driver: Driver is a cylindrical piece located at the other end of the Shank. It is made out of special alloy steel, and dimensionally according to industry standards. Driver has a concentric hole through its length for coolant to pass through in to the Shank. This also has an undercut or flat section for the set screw, which holds in the spindle bore. Two Flute Gundrills, with special nose geometry, are used for non-ferrous materials and allow for up to 80% increase in feed rates. The Working Principle of Gun Drilling Process: Long length of the Gundrill Shank is externally supported by bushes or bearings to avoid vibrations and to maintain the linearity, roundness precision and desired surface finish of the drilling operation. High pressure coolant, assuring sufficient flow rate, is pumped in to the Gundrill towards the cutting edge of the Carbide Tip, through the V- shaped fluted tubular shank. The coolant, this way reaches the machining zone. Thereby it cools and lubricates the cutting edges of the Tip and also the Shank supporting bearing area. The coolant flow also serves to pick up chips formed at the cutting edges and to transport them into the Chip Box, through the V-flute. Gun Drilling diameters have normal range between 1mm to max. 50 mm. Depth to Diameter Ratios vary according to the type of the drill and process being used. Ratio Cutting Tool & Process 5:1 Using common twist drills 10:1 Using high performance twist drills with through coolant 20:1 Using special deep hole drills with through coolant 100:1 Using Gundrills on dedicated Gundrilling machine 200:1 Using Gundrilling on high performance Gundrilling machine 300:1 Using Special nose geometry Gundrills in proprietary processes. What are the advantages of Gundrilling process? • Gundrilling is a single pass complete operation, which does not call for any subsequent operations, like reaming, honing, de-burring after its initial pass. • Constant flow of pressurised coolant not only transports chips into a chip box, but also keeps the cutting area and tool edges cool. Thereby increases tool-life considerably. Application of Gundrills in Industry Sectors: Mould-Industry, Aerospace, Automobile, Machine Tools, Paper Industry, Defence, Mining Tools, etc. Gundrills practically can be used in any industry wherein close tolerance long length holes need to be drilled in metal components. |
|
Company Prodcut:Accusharp Cutting Tools |
|
|